О КЛИНКАХ ЯПОНСКИХ МЕЧЕЙ БЕЗ ДОМЫСЛОВ. Часть 2
О КЛИНКАХ ЯПОНСКИХ МЕЧЕЙ БЕЗ ДОМЫСЛОВ. Часть 2
Продолжение. Начало в НОЖNEWS № 14
Получение стали
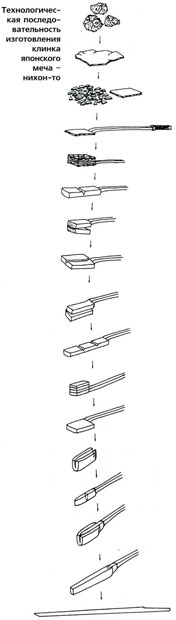
Процесс изготовления традиционного японского меча начинается с получения исходного продукта — стали. Ее получали из железосодержащего песка, добываемого в определенных местах. Песок этот содержал оксид железа и назывался сатэцу. Исходный материал обогащали, промывая водой и удаляя пустую породу, а после пережигали с древесным углем в сыродутной печи. В результате этого образовывался пористый кусок металла — крица. Ее измельчали и пережигали повторно, железо науглероживалось, превращаясь в сталь. Полученную массу проковывали, уплотняя металл. Во время этого процесса через поры выходили наружу вредные примеси в виде шлаков.
Затем полученную лепешку закаливали в воде и разбивали на мелкие осколки. По зернистости сколов, свидетельствующей о различном содержании углерода в отдельных осколках, их сортировали, сваривали, проковывая до тех пор, пока не образовывались более или менее однородные пластины металла. Таким образом, каждый кузнец изготавливал для себя исходный материал, сообразуясь со своим опытом. Таких кузнецов называли о-кадзи.
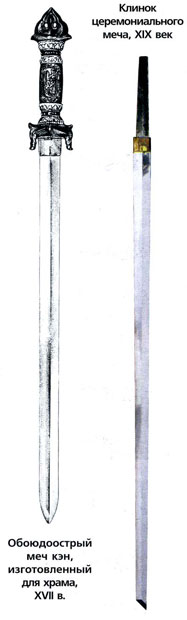
Второй способ получения сырья требовал специализации и усилий многих людей. Он происходил в печах, называемых татара. За один раз в печь загружали до 8 т сатэцу и 13 т древесного угля, получая в конце процесса стальной слиток кэра весом около 2 т. Этот слиток тащили по склону, возвышенности наверх и роняли на камни, в результате чего он разбивался на более мелкие части. Их подбирали, дробили, осколки сортировали и проковывали, сваривая между собой. Но этот процесс был более практичен, поскольку кэра уже состояла из стали, правда, науглероженной очень неравномерно, в пределах 0,6–1,5 % углерода. Сталь, полученная таким образом, называлась тамахаганэ, и именно она считается классическим исходным материалом для японских мечей. Получают ее и сейчас, как в древности, в таких же печах, используя традиционную технологию. При этом сатэцу в некоторых месторождениях природно легирован элементами, которые, входя в состав стали, улучшают ее свойства, делая клинки более качественными.
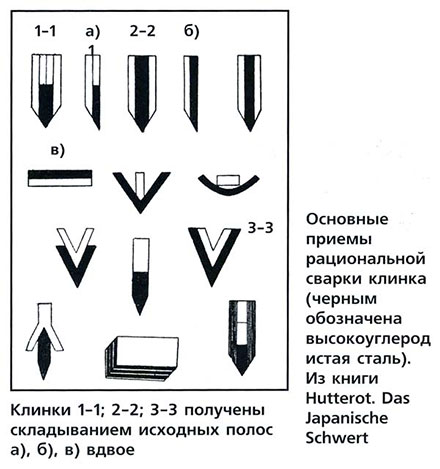
Кузнечные технологии
В отличие от о-кадзи, полностью контролировавших весь процесс получения исходного материала, кузнецов, работавших со сталью, получаемой в печах — татара, называли ко-кадзи. Из отсортированных на глаз мелких кусочков та-махаганэ ко-кадзи изготавливал методом кузнечной сварки брикеты металла разного качества. Разница была в содержании углерода. Но даже в каждом из отдельных брикетов содержание углерода не было равномерным, и поэтому при закаливании брикеты становились хрупкими из-за чрезмерных внутренних напряжений и как исходный материал для изготовления клинка не годились.
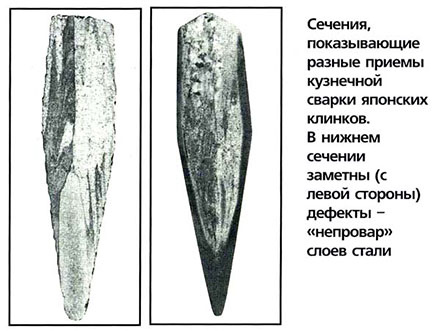
Вот с этого момента и начинается характерная японская технология, в принципе известная и в других частях света еще в древности, но нигде кроме Японии так скурпулезно не повторяемая в виду большого риска брака в случае некачественного «провара» слоев металла. Речь идет о так называемом «дамаске», многослойной стали, полученной путем кузнечной сварки.
Следует оговориться, что европейский дамаск, первоначально изготовлявшийся в Сирии, был всего лишь дешевой подделкой, имитацией индийского литого булата, обладавшего действительно уникальными качествами. Пакет из пластин стали с разным содержанием углерода проковывали, многократно скручивали, перемешивая слои и, в конечном итоге, сделанный из этой заготовки клинок протравливали слабым раствором кислоты. В результате этого железо разъедалось быстрее, а сталь медленнее, и на плоскостях образовывался рельефный узор, для неискушенного потребителя идентичный булатному. Эстетическая направленность, выраженная в необычайном узоре клинка, главенствовала над его качеством. И только гораздо позже мастера, изготовлявшие дамаск, смогли совместить «приятное с полезным», опытным путем найдя такие технологии, следуя которым изделия из Дамаска не так заметно проигрывали настоящему булату в качестве, будучи на уровне лучших европейских литых сталей. Но это тема отдельной статьи.
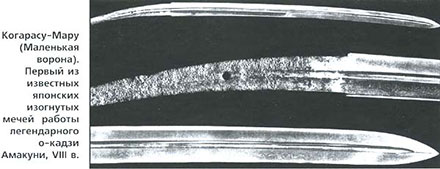
Здесь же следует подчеркнуть, что «японский дамаск» — многократная проковка заготовки — преследовала другую цель. Во-первых, проковывался один и тот же брикет стали. Он вытягивался, надрубался вдоль и складывался пополам, опять свариваясь, надрубался поперек, складывался… и так до 15 раз (но не больше). При 15-кратном проковывании образуется более 32 тысяч слоев металла, становящегося практически однородным, т. к. каждый слой достигает почти молекулярной толщины. С помощью этой операции достигается выравнивание химических и механических характеристик стального пакета, и поковка может противостоять более мощным механическим нагрузкам, т. к. из теории сопротивления материалов известно, что многослойный брус гораздо прочнее монолитного.
Для изготовления одного клинка кузнец изготавливал по подобной технологии несколько полос с различным содержанием углерода, которое задавалось сортировкой исходных осколков стали.
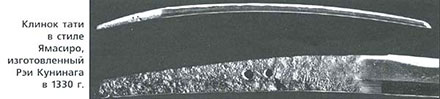
Полученный таким способом образец бесполезно травить кислотой, ведь по сути это один кусок стали, и разъедается он по всей поверхности с одинаковой скоростью. Поэтому узор на нем не выявится. Но в отполированной до зеркального блеска абсолютно гладкой поверхности глаз внимательного наблюдателя увидит рисунок выходящих наружу слоев — хада. Он образован эфемерной границей между слоями — диффузией молекул, вызванной кузнечной сваркой. Именно эта тонкая, можно сказать, микроскопическая работа, совершаемая с помощью кузнечных молотов, и составляет основную трудность всего процесса. Достаточно небольшой небрежности в работе: оставить отпечаток пальца или кусочек окалины (в этом месте образуется «непровар»), и все идет в брак.
Рациональная сварка
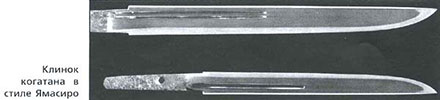
Процесс, описанный в предыдущей главе, был всего лишь подготовительным. В результате получалось несколько полос слоеной стали (минимум 2, максимум 7, в зависимости от принятого способа сварки клинка) с различным содержанием углерода. Сваривая их в различной комбинации, принятой в той или иной японской школе кузнечного искусства, в конечном результате и получали полосу японского меча. Обязательным условием было использование полосы с наибольшим содержанием углерода (до 1,5 %) для лезвия меча, а с наименьшим (до 0,5 %) для внутренней, скрытой боковыми накладками части клинка. При этом никогда внутри не использовалось низкосортное железо, способное изгибаться при малейшем усилии. Использование в конструкции рационально расположенных полос стали разного качества давало возможность японскому клинку уверенно противостоять механическим нагрузкам и в то же время иметь твердое лезвие, способное долго держать заточку. По сути, клинок японского меча имеет композитную конструкцию со всеми вытекающими из этого выгодами. В 30-х годах XX века известный историк оружия В.В Арендт, исследуя этот вопрос, назвал такой процесс «рациональной сваркой», что очень точно передает суть конечной операции.
Черновая обработка и закалка
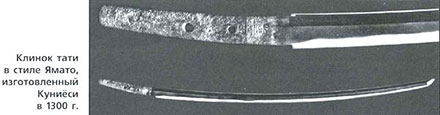
По окончании ковки, после того как полосе в общих чертах были преданы размеры и изгиб, она подвергалась отжигу. Будучи медленно нагретой в горне без доступа кислорода до температуры выше 800 °C, она затем так же медленно остывала вместе с горном. Потом полосу, ставшую мягкой и податливой, обрабатывали напильником и абразивными камнями, придавая ей окончательную форму. При этом режущую кромку лезвия не затачивали, оставляя ее притуплённой (толщиной 1–2 мм) для того, чтобы она могла сохранить равномерный нагрев в короткий промежуток времени, необходимый для переноса полосы из горна в сосуд с охлаждающей жидкостью. Если требовалось, инструментом, похожим на рубанок, простругивали долы вдоль обуха. Придавали форму хвостовику и наносили на него насечку. На этом подготовка клинка к самому главному процессу — закаливанию — считалась завершенной.
Перед закаливанием, которое производится в воде определенной температуры, клинок покрывают глиной. Глину перед этим надо хорошо отмутить, то есть удалить из нее посторонние примеси. Для того, чтобы получить совершенно однородную глину для обмазки клинков, в Японии изобрели свой способ.
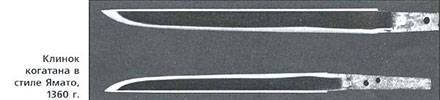
Для этого в морозный солнечный день влажные комки глины выкладывали на солнце. Влага, находящаяся в глине, замерзала и превращалась в лед. Лед, не переходя в воду, на солнце испарялся, и комья осыпались, образуя обезвоженный порошок. Его собирали, просеивали на мелком сите и, смешав с водой, получали лишенный примеси глинистый раствор требуемой консистенции.
Сначала весь клинок покрывают очень тонким слоем огнеупорной глины с добавками. Затем, отступив от кромки лезвия и от острия клинка, накладывают на боковые стороны и обух клинка слои потолще, давая каждому слою просохнуть. Суть этого процесса состоит в том, что толщиной слоя глины, нанесенного на клинок, регулируют скорость теплоотдачи при термообработке и контролируют весь процесс, закаливая различные участки клинка в разных режимах в течении того короткого промежутка времени, пока идет резкое остывание оружия в охлаждающей жидкости. Очень тонкий слой глины на лезвии позволяет закалить его с максимальной твердостью (50–65 ед. Роквелла). В тоже время остальные участки получаются более мягкими, но зато способными противостоять ударным нагрузкам. После нанесения слоев глины по всей длине клинка, на него в районе стыка лезвия с голоменью клинка (линия Хамон), на тонкий первоначальный слой подсохшей глины ребром шпателя наносят тонкие поперечные ребра из глины (аси-ножки). Смысл этого действа в том, что под нитеобразными утолщениями на тонком участке глины клинок закаливается в ином режиме, он менее твердый. В результате нарушается монолитность внутренней структуры закаленного металла. Практически это означает, что от выкрошившегося в процессе эксплуатации участка клинка трещины не идут дальше, «обрываются». Это продлевает жизнь клинку с боевыми дефектами, оставляя его таким же надежным, как и раньше.
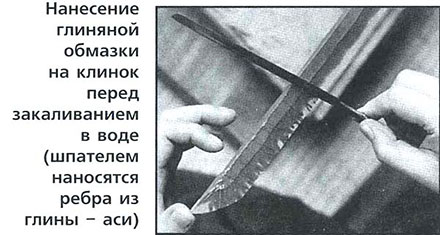
После очистки закаленного клинка от остатков глины его предварительно шлифуют достаточно грубым камнем, чтобы, осмотрев в белом виде, убедиться в отсутствии видимых дефектов. Если закаливание прошло удачно и явных дефектов нет, кадзи гравирует на хвостовике, оставшемся мягким, свое имя, название местности или что-то иное, что подсказывает его сердце и что поможет впоследствии потомкам идентифицировать клинок его работы. Кстати, великие мастера вообще не подписывали свои изделия, считая, что и так ясно, кто сотворил это рукотворное чудо! На риторический вопрос о том, какой временной промежуток нужен, чтобы отковать классический японский меч (нихон-то), соблюдая все технологии — ответ прост. Вопреки утверждениям о том, что на изготовление одного клинка уходят годы, организацией nbthk (общество по охране искусства японского меча) рекомендовано современным мастерам, работающим по традиционной технологии, не делать больше 24 клинков в течение года. Если учесть, что нормальный цикл работы — изготовление одновременно двух клинков (пока один прогревается, второй проковывается), то на изготовление одного клинка затрачивается месяц. При этом нельзя делать скоропалительный вывод, что если на два клинка затрачивается месяц, то на один уйдет 15 дней. Нельзя нагреть и проковать в два раза быстрее! Ускоренная технология ведет к браку. Поэтому изготовление одновременно двух клинков — это всего лишь рациональное использование времени.
Продолжение следует
Виктор Кленкин, «Клинок»
Более 800 000 книг и аудиокниг! 📚
Получи 2 месяца Литрес Подписки в подарок и наслаждайся неограниченным чтением
ПОЛУЧИТЬ ПОДАРОКЧитайте также
Таблица 1. Ощее описание популярных японских поварских моделей в европейском стиле
Таблица 1. Ощее описание популярных японских поварских моделей в европейском стиле [В виде
Часть 3 Окунь
Часть 3 Окунь «Гиганты и карлики» В формировании окуневых стай, а можно сказать, и в росте, существует одна неприятная для рыболова закономерность: внушительных размеров достигают, очевидно, процентов 10-15 от общего количества хищников в водоеме. Большинство окуневых
Часть 6 Сом
Часть 6 Сом Места обитания и нравы усатого «мафиози» Сом – крупнейший хищник наших водоемов. Сом встречается практически во всех крупных реках, озерах и водохранилищах России. Наибольшей численности эта теплолюбивая рыба достигает в бассейнах Каспийского, Аральского,
О КЛИНКАХ ЯПОНСКИХ МЕЧЕЙ БЕЗ ДОМЫСЛОВ. Часть 2
О КЛИНКАХ ЯПОНСКИХ МЕЧЕЙ БЕЗ ДОМЫСЛОВ. Часть 2 Продолжение. Начало в НОЖNEWS № 14Получение стали Процесс изготовления традиционного японского меча начинается с получения исходного продукта — стали. Ее получали из железосодержащего песка, добываемого в определенных
О КЛИНКАХ ЯПОНСКИХ МЕЧЕЙ БЕЗ ДОМЫСЛОВ. Часть 3
О КЛИНКАХ ЯПОНСКИХ МЕЧЕЙ БЕЗ ДОМЫСЛОВ. Часть 3 Продолжение. Начало в НОЖNEWS № 14 и 15Изображения на полосе меча На клинках и хвостовиках японских мечей, кроме надписей, часто встречаются изображения, различные по характеру, но всегда подчеркивающие индивидуальность
О КЛИНКАХ ЯПОНСКИХ МЕЧЕЙ БЕЗ ДОМЫСЛОВ
О КЛИНКАХ ЯПОНСКИХ МЕЧЕЙ БЕЗ ДОМЫСЛОВ В течение десяти столетий клинки японских мечей существуют без особых изменений в конструкции. Благодаря превосходным качествам этого вида холодного оружия, а также особому отношению японской нации к этим, казалось бы, сугубо
Отделка мечей
Отделка мечей Во все времена оружейники стремились применять богатую отделку. В начале XVI в. художники начали печатать эскизы для изготовителей ружей и торговцев мечами, чтобы они смогли использовать их для украшения и рекламы своих изделий. Так, Ганс Гольбейн-младший,
Часть I
Часть I
Часть II
Часть II Сегодня мы предлагаем вашему вниманию вторую часть записок оружейного мастера. Она посвящена основным принципам, согласно которым можно производить разборку и сборку образцов огнестрельного оружия без подробного