3. Отделка поверхностей деталей и изделий лакокрасочными материалами и облицовывание
3. Отделка поверхностей деталей и изделий лакокрасочными материалами и облицовывание
Подготовленную поверхность древесины покрывают лаками, красками или эмалями. Лаковая пленка придает изделию красивый внешний вид и защищает поверхность от влаги.
При непрозрачной отделке древесину окрашивают масляными красками – белилами и эмалями ПФ-14 на основе пентафталевых смол. Минимальная толщина пленки должна быть 50–70 мкм. Для окраски столярных изделий применяют цинковые белила.
Последовательность технологических операций, выполняемых при подготовке деталей к окраске масляными, эмалевыми и синтетическими красками поверхностей внутри помещений, следующая: очистка поверхностей, вырезка дефектов (сучков, засмолов) с расшивкой щелей, проолифка (огрунтовка), частичная подмазка с проолифкой подмазанных мест, шлифование подмазанных мест, первая окраска, вторая окраска, а при более высококачественной окраске – очистка, вырезка дефектов древесины, проолифка (огрунтовка), частичная подмазка с проолифкой подмазанных мест, шлифование подмазанных мест, сплошная шпатлевка, шлифование, огрунтовка, флейцевание, шлифование, первая окраска, флейцевание, шлифование, вторая окраска, флейцевание или торцевание.
Столярные изделия снаружи и внутри помещений окрашивают масляными, эмалевыми и эпоксидными красками. Столярные изделия внутри помещений и встроенную мебель окрашивают поливинилацетатными типа ПВА, масляными и акрилатными красками.
Поверхности деталей и изделий, окрашенные масляными, синтетическими, эмалевыми и лаковыми составами, должны иметь одинаковую фактуру – глянцевую или матовую. Пятна, отлипы, морщины, неровности, следы кистей, потеки и просвечивание нижележащих слоев краски, непрокраска не допускаются.
Нанесение лакокрасочных материалов вручную. На узкие поверхности (кромок) лаки, краски, эмали наносят ручниками – короткими круглыми щетинистыми кистями типа КР, на широкие поверхности – широкими плоскими кистями или малярными валиками. Вместо кистей можно использовать щетки, а также тампоны.
Лак наносят на сухую поверхность древесины, очищенную от пыли, равномерными слоями без потеков примерно 3–6 раз. Каждый слой лака до нанесения следующего нужно хорошо высушить. Изделие считается отделанным, если его поверхность имеет одинаковый и ровный блеск.
Высококачественные изделия отделывают полированием, так как полированная поверхность имеет устойчивый блеск и хороший вид.
Полирование выполняют ручным и механизированным способами. Для предохранения от загрязнения, высыхания и возгорания тампоны хранят в металлическом ящике.
Механизированное нанесение лакокрасочных материалов. Распыляют лакокрасочные материалы механическим и пневматическим способами. Наибольшее распространение получило пневматическое распыление, при котором под действием сжатого воздуха лакокрасочные материалы дробятся и в виде мелких частиц оседают на окрашиваемом изделии, растекаясь по его поверхности и образуя сплошное покрытие. Этот способ отделки древесины имеет и недостатки: для нанесения краски требуются специальные камеры, оборудованные вытяжными и очистными устройствами; при распылении до 20–40 % краски теряется на образование лакокрасочного тумана, который ухудшает санитарные условия труда.
Более совершенный способ отделки столярных изделий – окраска в электрическом поле высокого напряжения с последующей сушкой в терморадиационно-конвективных камерах. Сущность процесса окраски в электрическом поле высокого напряжения заключается в следующем: между окрашиваемым изделием, имеющим положительный заряд, и распыляемыми частицами лакокрасочных материалов, имеющими отрицательный заряд, создается постоянное электрическое поле высокого напряжения. Распыляемые частицы лакокрасочных материалов движутся по силовым линиям электрического поля и осаждаются на изделии. На рис. 127 показана схема окраски столярных изделий в электрическом поле высокого напряжения. Изделия навешивают на цепь конвейера, которым они подаются в камеру нормализации для покрытия специальным электропроводящим составом, затем этим же конвейером они направляются в камеру окраски. После окраски эмалями изделия поступают в терморадиационно-конвективную сушильную камеру.
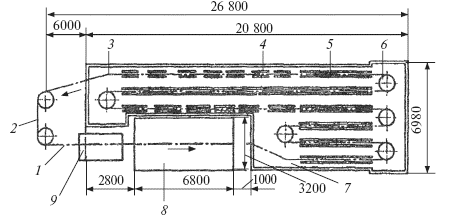
Рис. 127. Схема окраски столярных изделий в электрическом поле высокого напряжения: 1 – место навешивания изделий; 2 – место съема изделий; 3 – цепь конвейера; 4 – зона установки электронагревателей; 5 – зона конвективной сушки; 6 – звездочка; 7 – сушильная терморадиационно-конвективная камера; 8 – камера электроокраски; 9 – камера нормализации
На качество окраски столярных изделий в электрическом поле влияет влажность древесины. Так, при влажности ниже 8 % качество окраски ухудшается.
При окраске столярных изделий в электрическом поле высокого напряжения автоматизируются почти все процессы, значительно уменьшаются потери лакокрасочных материалов, улучшаются санитарно-гигиенические условия для работы в цехе, сокращаются площади для окраски и повышается качество окраски поверхности изделий.
Лакокрасочные материалы на столярные изделия наносят также методом струйного облива. Изделия (окна, двери) навешивают на подвесной конвейер, движущийся в камеру облива, где на поверхность наносится краска или эмаль, вытекающая из сопл под давлением до 0,1 МПа в виде струи. После окраски изделия поступают в камеру выдержки в парах растворителей. В этой камере помимо отекания излишков краски происходит равномерное распределение ее по всей поверхности изделия. Излишки краски, стекающие с изделий, по лотку поступают в сборники и после фильтрации – в систему облива. После выдержки в камере изделия поступают в конвективную многоходовую сушильную камеру. Недостаток метода струйного облива – плохая укрывистость кромок и несколько увеличенный расход краски.
Лакокрасочные материалы на плоские поверхности наносят на вальцовочных станках, которые входят в автоматические линии, где последовательно выполняют следующие операции: подогрев полотна дверей, грунтование, сушка, шлифование, подогрев полотна, лакирование, сушка. Плоские детали (щиты, двери, плиты) можно отделывать на лаконаливной машине (рис. 128). Основная часть машины – наливочная головка. Процесс нанесения лакокрасочных материалов наливом состоит в том, что уложенные на конвейер детали подаются им под наливочную головку, из которой в виде непрерывной завесы стекает лакокрасочный материал и покрывает детали равномерно по всей ширине одинаковым по толщине слоем краски, лака.
По сравнению с пневматическим распылением при обливе уменьшаются потери лакокрасочных материалов и улучшаются санитарные условия работы в цехе.
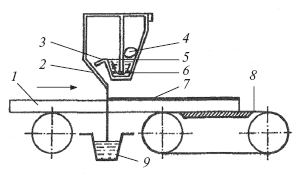
Рис. 128. Схема лаконаливной машины: 1 – деталь; 2 – экран; 3 – сливная плотина; 4 – коллектор; 5 – перегородка; 6 – фильтр; 7 – покрытие; 8 – конвейер; 9 – лоток
Сушка лакокрасочных покрытий. После нанесения лакокрасочных покрытий изделия сушат в сушильных камерах, которые в зависимости от конструкции подразделяются на конвективные, терморадиационные, терморадиационно-конвективные. Камеры могут быть проходными или тупиковыми.
Сроки высыхания лакокрасочных материалов зависят от вида красок, толщины слоя и температуры среды, в которой сушится покрытие. Ускорить высыхание лакокрасочного покрытия можно тремя способами: путем аккумулирования теплоты в древесине (предварительный подогрев древесины), конвективным и терморадиационным.
Процесс аккумулирования теплоты заключается в следующем: поверхность изделия перед окраской предварительно подогревают до температуры 100–105 °C, затем окрашивают и подают в другую камеру для сушки. Так как изделие было предварительно нагрето, при прохождении через вторую камеру растворители быстро испаряются и поверхность высыхает. Этот способ особенно эффективен при отделке быстросохнущими лакокрасочными материалами: сокращаются сроки сушки покрытия и расход растворителей.
При конвективной сушке теплота передается от источника к окрашенной поверхности воздухом, нагретым до 40–60 °C. Ввиду небольшой теплотворной способности воздуха теплота от окрашенной поверхности передается медленно, поэтому и поверхности изделий сохнут также медленно.
Более рациональным является терморадиационный способ сушки лакокрасочных покрытий, при котором ускоряется сам процесс сушки и требуются камеры меньших размеров. Процесс сушки сокращается за счет поглощения окрашиваемой поверхностью инфракрасных лучей, излучаемых нагретыми трубчатыми нагревателями.
Поверхность окрашенных изделий, поглощая инфракрасные лучи, нагревается, начиная с нижней части лакокрасочного покрытия, что дает возможность свободно испаряться нагретым растворителям.
Испаряясь и проходя через слой краски, растворители одновременно прогревают его, что вызывает интенсивное нагревание всего слоя краски и значительно ускоряет сушку.
Для облицовывания стен, перегородок применяют бумажно-слоистый пластик – листовой материал, получаемый путем прессования при высоком давлении специальных бумаг, которые пропитаны карбамидными или фенолформальдегидными смолами. Бумажно-слоистый пластик бывает разного цвета с глянцевой или полированной поверхностью. Он достаточно прочен, водостоек, долговечен, легко моется.
Пластик толщиной 1–1,6 мм крепят к поверхности на мастиках (КН-2, КН-3), а толщиной 2–3 мм – раскладками, прикрепляемыми к деревянному каркасу.
Отделывать поверхность стен, перегородок листами пластика начинают с нижнего ряда из угла помещения.
Листы стыкуют между собой как в вертикальном, так и в горизонтальном направлении.
До начала работ листы прирезают по размеру, прифуговывают кромки, проверяют правильность стыковки кромок. Мастику наносят на тыльную сторону листа равномерным слоем толщиной не более 1 мм. Намазанной стороной аккуратно без смещения и перекосов лист прикладывают к поверхности стены, после чего тряпкой притирают равномерно сначала в середине листа, а затем поочередно влево и вправо, вверх и вниз. Излишки мастики, грязь снимают тампоном, смоченным в ацетоне. Между листами оставляют руст (зазор в стене) шириной 5 мм. Положение листов до момента схватывания мастики фиксируют инвентарными прижимающими приспособлениями. Швы между листами окрашивают водоэмульсионными красками или заклеивают на мастике КН-2 поливинилхлоридной безосновной пленкой.
Для крепления листов пластика вместо мастики можно применять деревянные, поливинилхлоридные и металлические раскладки. Облицовку стен при этом начинают с угла помещения, прикрепляя вертикальную угловую и горизонтальную раскладки, выверяют их положение по отвесу и уровню, затем устанавливают первый лист и ставят вторую раскладку и т. д.
Фиксируют положение листов пластика на поверхности стены, перегородки до крепления раскладками гвоздями, забиваемыми в предварительно просверленные отверстия. По мере закрепления листов гвозди вытаскивают. Раскладки ставят так, чтобы они закрывали отверстия от гвоздей.
Раскладки крепят к стенам шурупами с шагом 150–200 мм, для чего в листах пластика по разметке высверливают отверстия диаметром немного большим, чем диаметр шурупа.
После облицовывания на поверхности бумажно-слоистого пластика не допускаются пятна, потеки мастики, царапины, пустоты между пластиком и стеной, перегородкой, вспучивание листов и т. п.
Более 800 000 книг и аудиокниг! 📚
Получи 2 месяца Литрес Подписки в подарок и наслаждайся неограниченным чтением
ПОЛУЧИТЬ ПОДАРОКДанный текст является ознакомительным фрагментом.
Читайте также
Глава 3 ОТДЕЛКА ПОВЕРХНОСТЕЙ СТОЛЯРНО-СТРОИТЕЛЬНЫХ ИЗДЕЛИЙ
Глава 3 ОТДЕЛКА ПОВЕРХНОСТЕЙ СТОЛЯРНО-СТРОИТЕЛЬНЫХ ИЗДЕЛИЙ 1. Виды отделки древесины Столярные изделия отделывают лакокрасочными материалами, предохраняющими их от воздействия окружающей среды. Окрашенные изделия имеют хороший внешний вид, их легче содержать в
2. Подготовка поверхностей деталей и изделий к отделке
2. Подготовка поверхностей деталей и изделий к отделке Столярная подготовка. Столярная подготовка включает заделку сучков, трещин, удаление грязи, зачистку поверхности древесины и последующее шлифование. Сучки и трещины заделывают вручную или на станках.Трещины в
Отделка плетеных изделий
Отделка плетеных изделий Чтобы повысить декоративные качества изделий, сделать более прочными и устойчивыми к неблагоприятным условиям, их покрывают жидкими отделочными материалами, облицовывают пленками и пластиками, украшают резьбой, выжиганием, накладным декором.
Техника безопасности при работе с лакокрасочными материалами
Техника безопасности при работе с лакокрасочными материалами При ведении покрасочных работ возможны следующие виды риска и опасности: опасность отравления и опасность пожара или взрыва. Опасность возникновения пожара может быть устранена или уменьшена при соблюдении
Декоративная отделка гипсокартонных поверхностей
Декоративная отделка гипсокартонных поверхностей Поверхности конструкций из гипсокартона поддаются разнообразной декоративной отделке. Качество подготовленных к отделке поверхностей должно удовлетворять следующим требованиям:• все работы по герметизации
Отделка изделий из дерева
Отделка изделий из дерева Для придания изделиям привлекательного товарного и эстетического вида они подвергаются отделке. Кроме этого, отделка, равно как и покрытие изделий различными пленочными материалами, защищает дерево от агрессивного воздействия окружающей
Механическая отделка изделий
Механическая отделка изделий Шлифование – это чистовая обработка поверхностей деталей абразивными инструментами. Шлифование металлических деталей осуществляют на шлифовальных станках вращающимися абразивными кругами, сегментами или брусками.Механический процесс
Отделка изделий из меди
Отделка изделий из меди Оксидирование меди азотной кислотой. Это один из старых, простых и надежных способов придания меди черного цвета.С помощью щетинной кисти на изделие наносят концентрированную азотную кислоту. При этом на поверхности изделия возникает бурная
Отделка изделий из латуни
Отделка изделий из латуни Химическая обработка придает латуни разнообразные цветовые тона: от желтых, оранжевых, красных до голубых, фиолетовых, синих и черных, причем на одном изделии можно получить переходные тона различных цветовых оттенков.Патинирование смесью
Отделка изделий из алюминия
Отделка изделий из алюминия Алюминий и его сплавы по химической природе значительно отличаются от других металлов и сплавов, наиболее часто применяемых в промышленности, как бы находясь на границе между металлами и неметаллами. Вследствие этого химические приемы
Отделка стальных изделий
Отделка стальных изделий Воронение стальных изделий. Красивый синий и синевато-черный тон с металлическим блеском образуются при оксидировании стальных изделий в растворе 400 г. едкого натра, 600 мл воды и по 10 г. калийной селитры и азотнокислого натрия. Изделие погружают
Отделка изделий из серебра
Отделка изделий из серебра Существует целый ряд рецептов для химической отделки изделий из серебра. Приведем наиболее простые.Черный цвет с синим оттенком получают при обработке изделий в подогретом до 60–70 °С растворе серной печени. Время обработки 3–5 мин. Черный,